Innovative Machine for Plastic Promises Enhanced Manufacturing Efficiency
By:Admin
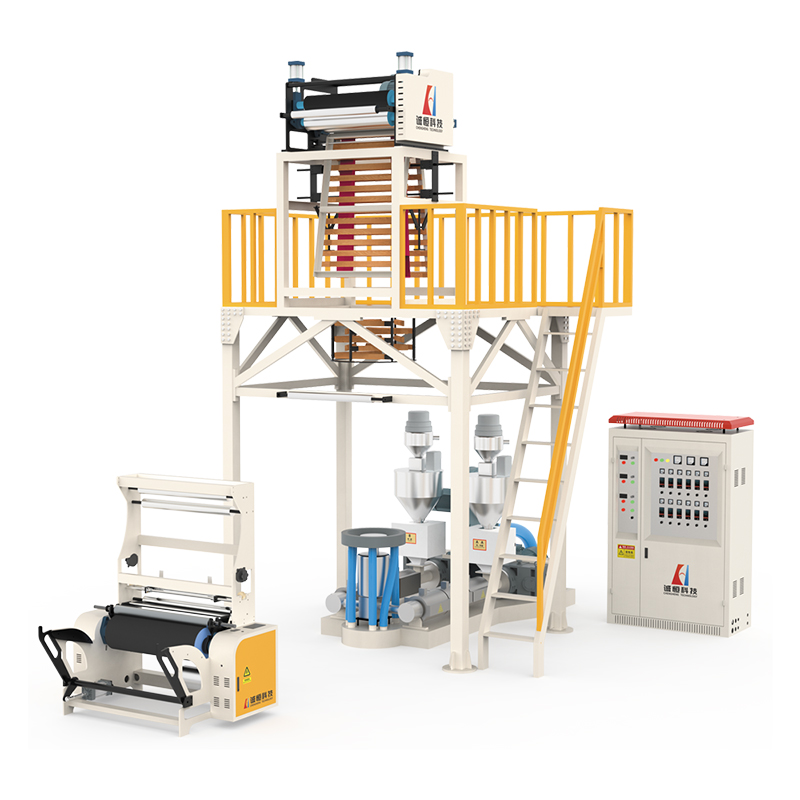
The PPS is a result of years of research and development by the company's highly skilled team of engineers and technicians. It is designed to offer unmatched precision, efficiency, and versatility in the production of a wide range of plastic products, from small components to large-scale items. The machine is equipped with advanced technology that allows for precise control over the production process, resulting in products that meet the highest standards of quality and consistency.
One of the key features of the PPS is its ability to process a variety of plastic materials, including PET, PVC, polyethylene, and more. This multi-material capability allows for greater flexibility in product design and manufacturing, enabling the company to meet the diverse needs of its clients across various industries. Additionally, the machine is equipped with automated processes that minimize the risk of human error and ensure that production runs smoothly and efficiently.
The company's commitment to sustainability is also evident in the design of the PPS. The machine is equipped with energy-efficient components that minimize power consumption and reduce the overall environmental impact of the manufacturing process. This aligns with the company's broader efforts to adopt sustainable practices and reduce its carbon footprint, in line with global efforts to combat climate change.
"We are thrilled to introduce the Plastic Production System to the market," said the company's CEO. "This machine represents a significant leap forward in plastic manufacturing technology, and we believe it will have a profound impact on the industry. We are confident that the PPS will enable us to better serve our clients and meet the growing demand for high-quality plastic products in a more sustainable manner."
The introduction of the PPS comes at a time when the demand for plastic products is on the rise across numerous industries, including packaging, automotive, electronics, and consumer goods. The company's investment in this innovative manufacturing technology underscores its commitment to meeting the evolving needs of its clients and maintaining a competitive edge in the market.
Moreover, the company has earned a reputation for delivering superior quality plastic products and providing exceptional customer service. Its team of experts works closely with clients to understand their specific requirements and develop customized solutions that meet their exact specifications. By continually investing in cutting-edge technology and refining its manufacturing processes, the company has positioned itself as a leader in the industry and a preferred partner for businesses seeking reliable and innovative plastic solutions.
As the company prepares to roll out the PPS, industry experts and clients alike are eager to see the impact that this new machine will have on the market. With its advanced capabilities and commitment to sustainability, the PPS is expected to set a new standard for plastic manufacturing and further solidify the company's position as a pioneer in the industry.
In conclusion, the introduction of the Plastic Production System marks a significant milestone for the company and the plastics manufacturing industry as a whole. This innovative machine represents the company's ongoing commitment to excellence, sustainability, and meeting the evolving needs of its clients. As the PPS enters the market, it is poised to make a lasting impact and further solidify the company's reputation as a leader in the production of high-quality plastic products.
Company News & Blog
The Ultimate Guide to Blown Film Moulding Process
The Blown Film Moulding Process is a crucial technique in the plastic manufacturing industry, and it has become an integral part of the production process for a wide range of products. This process is employed by many companies, one of which is {Company Name}. {Company Name} is a leading provider of plastic packaging solutions, and their expertise in the Blown Film Moulding Process has enabled them to produce high-quality products for various industries. With a focus on innovation and advanced technology, {Company Name} has established itself as a trusted partner for businesses seeking reliable and durable packaging solutions.The Blown Film Moulding Process involves extruding molten plastic through a circular die, which is then inflated to the desired thickness and shape using air. This results in a seamless tube of plastic, which can be used for various applications such as packaging films, bags, and other products. {Company Name} has mastered the art of the Blown Film Moulding Process, and they have integrated this technique into their production line to create a wide range of packaging solutions. Their state-of-the-art facilities and advanced machinery allow them to produce films of different properties, including high clarity, strength, and puncture resistance. In addition to their expertise in the Blown Film Moulding Process, {Company Name} also takes pride in their commitment to sustainability. They utilize eco-friendly materials and production methods to minimize their environmental impact, and they continuously seek ways to improve their processes to reduce waste and energy consumption.With a strong focus on quality and innovation, {Company Name} has been able to cater to the diverse needs of their clients across various industries such as food and beverage, pharmaceuticals, and retail. Their packaging solutions are designed to provide protection, durability, and convenience, making them a preferred choice for businesses looking for reliable packaging options.The Blown Film Moulding Process has played a crucial role in {Company Name}'s ability to deliver top-quality packaging solutions to their customers. By leveraging this technique, they have been able to create custom packaging solutions that meet specific requirements and exceed industry standards. Their ability to produce films with different properties and characteristics has allowed them to cater to a wide range of applications, demonstrating their versatility and expertise in the field.Furthermore, {Company Name} is dedicated to providing exceptional customer service, ensuring that their clients receive personalized support and guidance throughout the process. From concept development to final product delivery, they work closely with their customers to understand their needs and provide tailored solutions that exceed expectations.In conclusion, the Blown Film Moulding Process has been instrumental in {Company Name}'s success as a leading provider of plastic packaging solutions. Their expertise in this technique, combined with their commitment to innovation and sustainability, has enabled them to meet the needs of various industries and deliver high-quality products to their clients. As they continue to expand and refine their capabilities, {Company Name} is well-positioned to remain a key player in the plastic packaging industry.
Small Plastic Extrusion Machine: A Cost-Effective Solution for Plastic Production
Mini Plastic Extrusion Machine Revolutionizes Small-Scale ManufacturingIn today's rapidly evolving manufacturing industry, small-scale businesses are constantly seeking innovative solutions to improve their production processes and remain competitive in the market. The introduction of the Mini Plastic Extrusion Machine, by a leading industry player, has certainly revolutionized the way small-scale businesses approach plastic extrusion.The Mini Plastic Extrusion Machine is a compact and efficient solution designed to cater to the specific needs of small-scale manufacturers. With its user-friendly interface and precise control system, this innovative machine allows businesses to produce high-quality plastic products with ease and efficiency. The machine is equipped with advanced technology that enables it to extrude various types of plastic materials, including PVC, PE, PP, and more, making it a versatile solution for a wide range of applications.One of the key advantages of the Mini Plastic Extrusion Machine is its small footprint, which makes it ideal for businesses with limited space. Despite its compact size, the machine is capable of delivering high production output, making it a cost-effective solution for small-scale manufacturers. Additionally, the machine is designed for easy maintenance and can be operated with minimal training, allowing businesses to maximize their production capabilities without incurring significant operational costs.The Mini Plastic Extrusion Machine is also equipped with features that ensure consistent product quality and dimensional accuracy. Its precise temperature control system and unique screw design contribute to the production of uniform plastic products, meeting the stringent quality standards required in today's market. This level of precision is particularly crucial for businesses operating in industries such as construction, automotive, and packaging, where product quality is of utmost importance.The company behind the Mini Plastic Extrusion Machine has a strong reputation for delivering cutting-edge solutions in the plastic extrusion industry. With a rich history of innovation and a commitment to customer satisfaction, the company has established itself as a leading player in the global manufacturing sector. Leveraging its extensive expertise and state-of-the-art facilities, the company has successfully developed the Mini Plastic Extrusion Machine to address the specific needs of small-scale businesses, offering them a competitive edge in the market.Furthermore, the company provides comprehensive technical support and after-sales services to ensure that businesses can maximize the performance of the Mini Plastic Extrusion Machine. This includes professional installation, training, and ongoing maintenance to keep the machine operating at its optimal level. By partnering with the company, businesses can benefit from a reliable and dedicated support system that helps them overcome any challenges they may face in their production processes.The introduction of the Mini Plastic Extrusion Machine has undoubtedly reshaped the landscape of small-scale manufacturing. With its compact design, advanced technology, and focus on product quality, the machine has empowered small-scale businesses to enhance their production capabilities and compete effectively in the market. As the manufacturing industry continues to evolve, innovative solutions such as the Mini Plastic Extrusion Machine will play a pivotal role in driving the growth and success of small-scale manufacturers around the world.
Your Ultimate Guide to Plastic Film Blowing: Types, Uses and Benefits
Plastic Film Blowing is a process used to create plastic films of various thickness and sizes. It involves melting down plastic resin and extruding it through a circular die, which then expands into a tube of molten plastic. This tube is subsequently inflated with air, cooled, and then flattened into a film. The process is widely used in the packaging industry to create materials such as grocery bags, shrink wrap, and industrial liners, among other products.One of the leading companies in the plastic film blowing industry is {}. With decades of experience and a commitment to innovation, they have established themselves as a key player in the market. Their state-of-the-art facilities and advanced machinery enable them to produce high-quality plastic films that meet the needs of their diverse customer base.The company's dedication to research and development has allowed them to stay ahead of the curve in terms of technology and product offerings. They continually invest in new equipment and processes to improve their production capabilities and enhance the performance of their plastic films. This commitment to innovation has earned them a reputation for reliability and excellence within the industry.In addition to their focus on technology, the company places a strong emphasis on sustainability. They are committed to minimizing their environmental impact and have implemented various initiatives to reduce waste, energy consumption, and emissions. Through responsible manufacturing practices and the use of eco-friendly materials, they are working towards a more sustainable future for the industry and the planet.Their dedication to quality and sustainability has not gone unnoticed. They have received numerous accolades and certifications for their commitment to excellence and environmental stewardship. This recognition further solidifies their position as a trusted and respected leader in the plastic film blowing industry.Looking ahead, the company is focused on expanding their product offerings and exploring new markets. They are continuously exploring new trends and consumer demands to stay ahead of the competition and meet the evolving needs of their customers. Additionally, they are working to further enhance their sustainability efforts and develop more eco-friendly options for their plastic films.With their track record of success and their unwavering commitment to innovation and sustainability, it is clear that {} will continue to be a dominant force in the plastic film blowing industry for years to come. Their dedication to quality, technology, and environmental responsibility sets them apart and positions them as an industry leader. As the demand for high-quality, sustainable plastic films continues to grow, {} is well-positioned to meet and exceed those needs, driving the industry forward and setting new standards for excellence.
High-Density Polyethylene Blown Film Extrusion: What You Need to Know
The leading manufacturer in the plastic extrusion industry, {} is proud to announce the expansion of their product line with the addition of HDPE blown film extrusion. This new offering provides customers with a wider range of options for their packaging and film needs, further solidifying {}'s position as a one-stop shop for all things plastic extrusion.HDPE, or high-density polyethylene, is a highly versatile and commonly used material in the packaging industry. It offers excellent strength and durability, making it the ideal choice for a wide range of applications. With the addition of HDPE blown film extrusion to their product line, {} is able to cater to the diverse needs of their customers, providing them with a superior packaging solution.{}'s state-of-the-art blown film extrusion process ensures that the HDPE film produced is of the highest quality. The company prides itself on using the latest technology and industry best practices to manufacture products that meet and exceed customer expectations. This commitment to quality is what sets {} apart from other plastic extrusion manufacturers, and it is a key factor in the company's continued success.In addition to their cutting-edge technology, {} is also known for its strong commitment to sustainability. The company understands the importance of minimizing its environmental impact, and as such, has implemented various eco-friendly initiatives in its manufacturing processes. With the introduction of HDPE blown film extrusion, {} is able to offer customers a sustainable packaging solution that is not only high-quality but also environmentally responsible.With the expansion of their product line, {} is poised to further solidify its position as a leader in the plastic extrusion industry. The company's dedication to innovation, quality, and sustainability sets it apart from its competitors and allows it to meet the ever-evolving needs of its customers."We are thrilled to announce the addition of HDPE blown film extrusion to our product line," said [Spokesperson's Name], [Title] at {}. "This new offering is a testament to our commitment to providing our customers with the best possible solutions for their packaging needs. We are confident that our HDPE film will exceed expectations and we are excited to see the positive impact it will have on the industry."With the introduction of HDPE blown film extrusion, {} continues to demonstrate its dedication to meeting the diverse needs of its customers. The company's unwavering commitment to quality, innovation, and sustainability sets it apart as a leader in the plastic extrusion industry, and with this latest expansion, {} is well-positioned to continue its success in the market.
How Blown Film Moulding Works: A Step-by-Step Guide
Blown Film Moulding Process is a key technology used by manufacturers to produce plastic films and sheets for a wide range of applications. By utilizing this advanced molding process, {} has solidified its position as a leading provider of high-quality plastic packaging solutions.The Blown Film Moulding Process involves melting plastic resin and then blowing it into a bubble with the help of air. This process allows for the creation of thin, continuous films that can be used in various industries such as food packaging, agriculture, construction, and medical packaging. The flexibility and efficiency of this process make it an ideal choice for producing films with specific properties such as strength, barrier protection, and optical clarity.{} has been at the forefront of innovating the Blown Film Moulding process, leveraging cutting-edge technology and expertise to create customized solutions for its customers. With a strong focus on research and development, the company has consistently improved its manufacturing processes to deliver films that meet the highest standards of quality and performance.One of the key advantages of {}'s Blown Film Moulding Process is its ability to accommodate a wide range of raw materials, including LDPE, LLDPE, HDPE, and PP resins. This versatility allows the company to cater to diverse market needs and produce films with different properties and characteristics. Whether it's for food packaging that requires excellent sealability and moisture resistance, or for industrial applications that demand high strength and puncture resistance, {} has the capabilities to deliver tailored solutions.In addition to its technical expertise, {} is committed to sustainability and environmental responsibility. The company has implemented state-of-the-art recycling and waste reduction initiatives to minimize its environmental footprint. By leveraging the Blown Film Moulding Process, {} can optimize material usage and reduce waste, contributing to a more sustainable and eco-friendly manufacturing process.The applications of the Blown Film Moulding Process are vast and varied. {}'s plastic films find applications in the packaging of food products, pharmaceuticals, and industrial goods. The films are also used in the agricultural sector for greenhouse films, mulch films, and silage bags. With the ability to produce films in various widths, thicknesses, and colors, {} can meet the specific requirements of its customers across different industries.Moreover, {}'s commitment to quality and customer satisfaction sets it apart in the market. The company adheres to stringent quality control measures at every stage of the manufacturing process, ensuring that its films meet international standards for safety and performance. With a customer-centric approach, {} works closely with its clients to understand their needs and provide them with customized solutions that add value to their products and operations.In conclusion, {}'s expertise in the Blown Film Moulding Process has established the company as a trusted partner for high-quality plastic packaging solutions. By leveraging advanced technology, a commitment to sustainability, and a customer-centric approach, {} continues to lead the way in delivering innovative and customized films for diverse applications. As the demand for high-performance plastic films continues to grow, {} is well-positioned to meet the evolving needs of its customers and the market.
Effective Plastic Screw Extruder Guide: All You Need to Know
Plastic Screw Extruder Innovations to Revolutionize Manufacturing IndustryWith the increasing demand for sustainable and efficient manufacturing processes, the plastic extrusion industry has been continuously seeking breakthrough innovations to meet these challenges. One company has been at the forefront of this movement, leading the way with their cutting-edge Plastic Screw Extruder technology. This technology promises to revolutionize the manufacturing industry, offering a more cost-effective and environmentally friendly solution for plastic extrusion processes.The Plastic Screw Extruder, developed by [Company], is an innovative piece of equipment that has been designed to address the limitations of traditional extrusion methods. The technology offers improved performance, higher production speeds, and enhanced sustainability, making it an ideal solution for a wide range of applications.[Company] is known for its expertise in the design and manufacturing of extrusion machinery, and the development of the Plastic Screw Extruder is a testament to their commitment to innovation and excellence. The company has a proven track record of delivering high-quality equipment to the industry, and their continued investment in research and development has enabled them to stay ahead of the competition.The Plastic Screw Extruder is equipped with state-of-the-art features that set it apart from traditional extrusion equipment. It utilizes advanced materials and engineering techniques to deliver superior performance, while also minimizing energy consumption and waste generation. This makes it a highly efficient and sustainable solution for manufacturers looking to improve their operations.One of the key advantages of the Plastic Screw Extruder is its ability to extrude a wide range of plastic materials, including high-temperature polymers and recyclable thermoplastics. This versatility makes it suitable for various industries, such as packaging, construction, automotive, and medical devices, where different types of plastics are used in manufacturing processes.Furthermore, the technology offers a higher degree of process control and customization, allowing manufacturers to achieve precise output specifications with greater consistency. This level of control is essential for achieving high-quality products and meeting the stringent requirements of modern industries.In addition to its technical capabilities, the Plastic Screw Extruder also delivers significant cost savings for manufacturers. Its efficient design and operation result in reduced downtime, lower maintenance costs, and improved overall productivity. This makes it a highly attractive investment for companies looking to optimize their production processes and remain competitive in the market.The environmental benefits of the Plastic Screw Extruder are also worth noting, as it significantly reduces the carbon footprint of plastic extrusion operations. By consuming less energy and generating less waste, manufacturers can minimize their impact on the environment while maintaining sustainable manufacturing practices.As a result of these advantages, the demand for the Plastic Screw Extruder is expected to increase significantly in the coming years. Manufacturers are increasingly recognizing the value of investing in advanced extrusion technology to improve their operations and stay ahead of the competition.In conclusion, the Plastic Screw Extruder developed by [Company] represents a major advancement in plastic extrusion technology, offering a more sustainable, efficient, and cost-effective solution for manufacturers. With its innovative features and proven performance, it is poised to revolutionize the manufacturing industry and set new standards for plastic extrusion processes. [Company] continues to lead the way in delivering cutting-edge solutions to the market, and the Plastic Screw Extruder is a testament to their commitment to innovation and excellence.
The Process of Film Extrusion: What You Need to Know
Tubular film extrusion is a process used to create a wide variety of plastic films and sheets by continuously forming and cooling the material through a cylindrical die. This method is highly efficient and cost-effective, making it a popular choice for companies in the packaging, construction, and agriculture industries. One leading provider of tubular film extrusion solutions is {brand name removed}, a global leader in the manufacturing and distribution of plastic packaging and films.{Brand name removed} has been at the forefront of tubular film extrusion technology for over 30 years, continuously innovating and improving their processes to meet the evolving needs of their customers. With state-of-the-art facilities and a team of experienced engineers and technicians, {brand name removed} is able to produce high-quality tubular films that are tailored to specific applications and requirements.One of the key advantages of tubular film extrusion is its ability to produce films in a wide range of sizes, thicknesses, and materials. This versatility allows {brand name removed} to cater to a diverse customer base, providing packaging solutions for food, beverages, pharmaceuticals, and industrial products. In addition, their tubular films are used in construction and agriculture for applications such as greenhouse coverings, mulch films, and protective packaging.{Brand name removed} is committed to sustainability and environmental responsibility, and their tubular film extrusion processes reflect this commitment. By using recyclable and biodegradable materials, as well as optimizing production processes to minimize waste and energy consumption, {brand name removed} ensures that their tubular films have a minimal impact on the environment. This eco-friendly approach has allowed them to become a trusted partner for companies seeking sustainable packaging solutions.Furthermore, {brand name removed} is dedicated to meeting the highest quality standards in their tubular film extrusion processes. Their films undergo rigorous testing to ensure that they meet the necessary strength, durability, and barrier properties required for their intended applications. As a result, customers can rely on {brand name removed} to deliver tubular films that provide excellent protection and performance for their products.In addition to their focus on quality and sustainability, {brand name removed} prides itself on its ability to offer customized tubular film solutions. Their engineering team works closely with customers to understand their specific needs and develop films that are tailored to their unique requirements. This collaborative approach has enabled {brand name removed} to build strong, long-lasting partnerships with a wide range of industries, providing them with the packaging solutions they need to succeed.Looking ahead, {brand name removed} continues to invest in research and development to further enhance their tubular film extrusion capabilities. By staying at the forefront of technological advancements and market trends, {brand name removed} is well-positioned to meet the evolving needs of their customers and provide innovative solutions for packaging and film applications. Their commitment to excellence, sustainability, and customer satisfaction makes them a trusted leader in the tubular film extrusion industry.In conclusion, tubular film extrusion is a versatile and efficient process that plays a crucial role in the production of plastic films for a wide range of applications. With its dedication to quality, sustainability, and customization, {brand name removed} has established itself as a leading provider of tubular film solutions, serving the needs of industries around the world. As the demand for high-performance and environmentally friendly packaging continues to grow, {brand name removed} is well-equipped to meet these needs and remain a key player in the tubular film extrusion market.
Understanding the Cost of Blow Moulding Machines
, excluding any proprietary information. Blow Moulding Machine Cost is a crucial factor for companies involved in the manufacturing of plastic products. The cost of a blow moulding machine can have a significant impact on the overall production expenses and ultimately the competitiveness of the products in the market. With the demand for high-quality and cost-effective blow moulding machines on the rise, companies are constantly looking for reliable suppliers that offer competitive pricing and advanced technology.One such company that has been making waves in the blow moulding machine industry is {}. Founded in {}, the company has quickly established itself as a leading manufacturer and supplier of blow moulding machines. With a strong focus on innovation, quality, and customer satisfaction, {} has earned a reputation for delivering cutting-edge solutions that meet the evolving needs of the industry.The company's extensive range of blow moulding machines caters to a wide spectrum of applications, including the production of bottles, containers, drums, and other plastic products. From high-speed machines for mass production to versatile models for small-scale operations, {} offers a comprehensive selection to suit diverse production requirements. Each machine is engineered with precision and incorporates the latest technological advancements to ensure efficiency, reliability, and minimal downtime.When it comes to blow moulding machine cost, {} is committed to providing competitive pricing without compromising on quality. The company understands the significance of cost-effectiveness in today's competitive market and strives to offer value-driven solutions that enable businesses to achieve higher productivity and profitability. By leveraging its expertise and resources, {} optimizes its manufacturing processes to keep the production costs in check, allowing it to pass on the benefits to its customers.In addition to the initial investment in the machine, the total cost of ownership is a critical consideration for businesses. {} is cognizant of this aspect and focuses on delivering machines that are not only affordable to procure but also economical to operate and maintain in the long run. The company's commitment to durability, performance, and ease of maintenance ensures that its machines deliver a compelling return on investment over their operational lifespan.Moreover, {} offers flexible financing options and responsive after-sales support, further enhancing the overall value proposition for its customers. Whether it's technical assistance, spare parts, or training, the company's dedicated team is always available to provide prompt and effective solutions, contributing to the smooth and uninterrupted operation of its machines.With a global footprint, {} serves a diverse clientele spanning various industries and geographies. The company's ability to tailor its offerings to meet specific customer needs and local market requirements has been instrumental in its success. By fostering strong partnerships and collaborations, {} continues to expand its reach and reinforce its position as a preferred choice for blow moulding solutions.In conclusion, the cost of a blow moulding machine is a critical factor that influences the competitiveness and profitability of businesses involved in plastic product manufacturing. {}. With its commitment to quality, innovation, and customer satisfaction, the company is well-positioned to address this pivotal aspect and deliver cost-effective solutions that empower its customers to thrive in the market. As the demand for advanced blow moulding technology continues to grow, {} remains at the forefront, driving the industry forward with its compelling value proposition.
Guide to Ldpe Plastic Film: Uses, Benefits, and Disposal Tips
The demand for LDPE plastic film has been on the rise in recent years due to its versatility and wide range of applications. LDPE, which stands for Low-Density Polyethylene, is a type of plastic that is commonly used in packaging, agriculture, and construction. Its flexibility, durability, and moisture resistance make it an ideal choice for various industries.In response to the increasing demand for LDPE plastic film, {Company Name} has emerged as a leading manufacturer and supplier in the market. With state-of-the-art facilities and a strong commitment to quality, {Company Name} has been able to meet the needs of its customers and establish itself as a trusted name in the industry.{Company Name} offers a wide range of LDPE plastic film products, including packaging film, agricultural film, and construction film. The company's advanced production technologies and stringent quality control measures ensure that its products meet the highest standards of performance and reliability.One of the key advantages of {Company Name}'s LDPE plastic film is its sustainability. The company is committed to environmental responsibility and has implemented eco-friendly manufacturing processes to minimize its carbon footprint. By using recycled materials and reducing waste, {Company Name} is contributing to the global effort to create a more sustainable and eco-friendly future.Furthermore, {Company Name} prioritizes customer satisfaction and aims to provide tailored solutions to meet the unique requirements of each client. Whether it's custom sizing, printing, or specialized performance attributes, the company goes above and beyond to deliver products that exceed expectations.In addition to its product offerings, {Company Name} is also dedicated to research and development, continuously exploring new ways to improve the performance and sustainability of its LDPE plastic film. By staying at the forefront of technological advancements, the company ensures that its customers have access to the latest innovations in the industry.{Company Name} has also established a strong global presence, serving customers in various markets across the world. Its commitment to excellence, reliability, and customer-centric approach has enabled the company to build long-lasting partnerships with clients and distributors worldwide.As the demand for LDPE plastic film continues to grow, {Company Name} remains at the forefront of the industry, providing high-quality products and exceptional service to its customers. With its focus on sustainability, innovation, and customer satisfaction, the company is poised to remain a leader in the market for years to come.In conclusion, {Company Name} has proven to be a reliable and forward-thinking manufacturer and supplier of LDPE plastic film. With its cutting-edge technologies, commitment to sustainability, and customer-centric approach, the company has set a new standard of excellence in the industry. As the demand for LDPE plastic film continues to expand, {Company Name} is well-positioned to meet the evolving needs of its customers and contribute to a more sustainable future.
Top Tips for Successful Blown Film Production
Blown Film Production: A Key Component of Company's Commitment to InnovationIn the world of manufacturing, {Company Name} has set itself apart as a leading innovator in the production of blown film. With a commitment to excellence and a focus on cutting-edge technology, the company has established itself as a key player in the industry.Blown film production is a crucial part of {Company Name}'s manufacturing process. This method allows for the production of high-quality, reliable film that is used in a wide variety of applications, including packaging, agriculture, construction, and more. By utilizing state-of-the-art equipment and employing a team of skilled professionals, {Company Name} is able to produce blown film products that meet and exceed the needs of their customers.One of the key advantages of blown film production is its versatility. The process allows for the creation of film in a wide range of thicknesses, widths, and properties, making it suitable for a diverse array of industries and applications. This flexibility is a major selling point for {Company Name}, as it allows them to cater to the unique needs of each of their clients.In addition to versatility, blown film production offers a number of other benefits. The process allows for precise control over the properties of the film, including its strength, durability, and transparency. This level of control ensures that {Company Name} is able to consistently produce film that meets the highest standards of quality.Another important aspect of {Company Name}'s blown film production is their commitment to sustainability. The company has made significant investments in research and development to ensure that their manufacturing processes are as environmentally friendly as possible. This includes implementing energy-efficient equipment, reducing waste, and exploring new materials and techniques that minimize the environmental impact of their operations.{Company Name} has also made significant investments in quality control and testing to ensure that their blown film products meet the highest standards of performance and reliability. This commitment to quality extends to every aspect of their manufacturing process, from raw material sourcing to final product inspection. As a result, {Company Name} has built a reputation for delivering blown film products that are dependable and consistent.As part of their ongoing commitment to innovation, {Company Name} continues to explore new advancements in blown film production. This includes the adoption of new technologies, the development of new products, and the expansion of their capabilities. By staying at the forefront of industry trends and developments, {Company Name} is able to offer their customers the latest and greatest in blown film technology.In conclusion, blown film production is a crucial component of {Company Name}'s commitment to innovation. By leveraging cutting-edge technology, a skilled workforce, and a dedication to quality and sustainability, the company has established itself as a leader in the production of blown film. With their ongoing dedication to excellence and forward-thinking approach, {Company Name} is well-positioned to continue delivering high-quality blown film products to their customers for years to come.